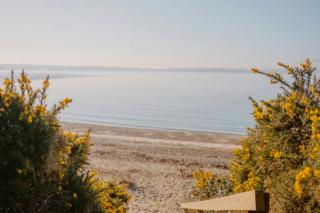
Hazard identification and risk assessment – early and late lifecycle activities
- Post Date
- 22 January 2023
- Read Time
- 2 minutes
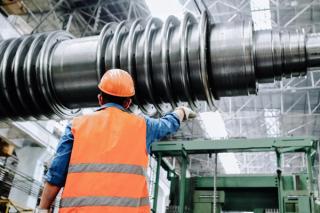
Within the field of process safety there are regulatory requirements to perform hazard identification and risk assessment (HIRA) using techniques which fall under the generic banner of process hazard analysis (PHA). The most prevalent form of PHA is the Hazard and Operability (HAZOP) study technique, however most companies’ understanding of this technique comes from HAZOP #3 rather than earlier or later HAZOP lifecycle phases.
Early HAZOP Stages – HAZOP#1
By the time that the HAZOP#3 is conducted, many opportunities to reduce risks have already been lost which could in turn lead to more expensive engineering costs to manage risks which could have been eliminated at earlier HAZOP stages. Operators within the high hazard industries are required to demonstrate that “all measures necessary” have been taken to prevent, control and mitigate major accident hazards. A fundamental part of this demonstration is compliance with accepted good practice and the implementation of inherently safer design principles when at the design stages. Early phase HAZOP studies such as HAZOP#1 use checklist approaches to quickly screen through proposed designs and to look for risk reduction opportunities at the inherent safety level of the hierarchy of risk.
Late HAZOP Stages – HAZOP#6
For both newly installed and existing plants and processing facilities there is a requirement for an on-going review of PHA’s which includes the consideration of operational experience and review of past accidents. Such requirements should be driven by the companies’ procedures for the management of risk assessments and are typically performed as a HAZOP#6. Functional safety standards, such as BS EN 61511 2017, also require FSA stage 4, a part of which includes a review of the underlying PHA.
For new plants and processes, this might at first seem excessive since they should have already been subjected to rigorous PHA’s / HAZOP studies prior to commissioning. Such studies, however, are based upon assumptions which might not be correct and only reveal themselves after a period of operation whereby without correction can lead to process operators “making do” and finding “workarounds”. For existing plants, a deterioration of safeguards over time can occur in addition to the changing nature of what constitutes accepted good practice.
In both instances, the re-review process is rooted in accepted good practice and is an essential part of asking “what more can I do to reduce risks” and, as such, is integral in demonstrating that all measures necessary have been taken to prevent, control or mitigate major accident hazards.
For more information or to discuss how we can help your business please get in touch.