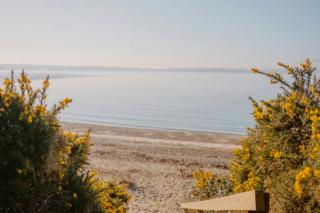
All measures necessary: how COMAH sites can demonstrate their approach to risk management
- Post Date
- 28 January 2023
- Read Time
- 2 minutes

Operators within the high hazard industries are typically regulated under the Control of Major Accident Hazards (COMAH) Regulations along with the Dangerous Substances and Explosives Atmospheres Regulations (DSEAR). The goal setting approach to UK legislation can cause confusion whereby operators are expected to demonstrate that they have taken all measures necessary to prevent, control or mitigate a major accident, without understanding what this means. The result of this is often that legal actions are raised not because a site is unsafe, but because the site can not confidently make the demonstration that is required.
The term “all measures necessary” does not require the operator to implement every risk reduction option which is technically possible or that can be thought of. In practical terms, demonstrating that all measures necessary have been taken is the same as demonstrating that the sites risks have been reduced to as low as is reasonably practicable (ALARP). A demonstration of ALARP is multi-faceted and changes dependent upon whether an establishment is already in existence or is in the process of being designed. Demonstrations of ALARP will require the following considerations:
- What is the current accepted good practice and are we applying such practices?
- What are the hazards and risks, what more could we do to reduce these risks?
- Of the risk reduction measures that we are not adopting, what is the justification for not doing so?
In some instances, reducing risks might require significant investment which is grossly disproportionate to the level of risk reduction expected. This, however, is not always the case and significant risk reduction can be achieved by implementing organisational and procedural measures which are rooted in accepted good practice. Since such measures are low cost, it would be difficult to argue that they are not reasonable.
By way of example, many operating companies will be familiar with, and have, a HAZOP study (typically HAZOP #3) but will fail to implement early and late lifecycle studies such as HAZOP stages #1 or #6, which are equally important in making a demonstration of all measures necessary. Likewise, where safety instrumented systems are utilised, a focus is often placed upon specification, design and installation and yet later lifecycle activities such as Functional Safety Assessment Stage 4 are missed.
In both cases, these organisational measures are rooted in accepted good practice and act to verify the assumptions within previous process safety risk assessments to provide “real world” risk reductions. With relatively low implementation costs such measures would be considered reasonable to perform and, therefore, form a part of any demonstration of “all measures necessary”.
Visit our Safety Advisory page to learn more about our services and how we can support you.