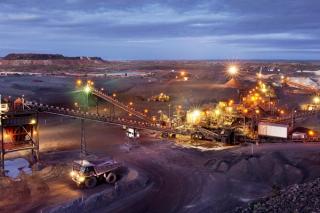
Metallurgical testwork for Viscaria copper-iron mine project
- Client Name
- Viscaria
- Location
- Kiruna, Sweden

Challenge
The client required a process flowsheet for their pre-feasibility study. SLR assisted with this by undertaking a programme of testwork on master composite samples representing the three ore bodies of their project.
The project is unique in that the client plans on processing three different ore bodies, each with their own metallurgical challenges. The testwork is therefore required to reflect what is achievable in a processing plant in terms of the flexibility of operating parameters while achieving optimal metallurgical performance.
The client is currently in the process of producing a feasibility study. This requires a higher level of understanding and confidence across their deposit and ore bodies individually. The client was uncertain how variability across the ore bodies may affect metallurgical performance.
Processing different ore bodies separately through a plant requires stockpiling of certain ore material while the plant is set up to process another. There is a degree of uncertainty regarding how the metallurgical performance of ore from certain areas of the deposit may be affected from stockpiling over time. This extent of this was required to be investigated in order to allow the client to mine plan appropriately, without negatively impacting plant performance.
Minimising the effect on the environment is at the forefront of the client’s objectives. This was critical when investigating froth flotation parameters which can include harmful reagents.
Solution
The flowsheet development testwork programme resulted in optimised flotation conditions that achieved grade and recovery targets which were previously unachievable in prior testwork programmes. As part of the flowsheet development, grind and re-grind sizes for froth flotation and magnetic separation processes were investigated and optimal sizes were identified.
Our testwork has investigated and identified the optimal processing methods for each ore body, within the constraints of processing them within the same processing plant.
The client’s exploration drilling identified areas of variability within the three ore bodies. Comminution, mineralogy, froth flotation, and magnetic separation testwork programmes were undertaken by SLR to investigate the impact of geological and spatial domains of the ore bodies regarding metallurgical performance. Mineralogy was used to explain underperforming samples and froth flotation parameters were modified to bring the variability samples back within target grades and recoveries.
Froth flotation reagents with minimal eco-toxicological properties were prioritised and dosages minimised when investigating froth flotation conditions. Specialised equipment was obtained by SLR to analyse the residual reagents in the process water to assist the client aligning with environmental regulations.
SLR collaborated with the client to develop a methodology to simulate and investigate the effect that stockpiling may have on their ores so they can develop a mine plan with confidence.
The large range of metallurgical testwork capabilities that SLR has accumulated allows a holistic approach when managing a project with multiple testwork programmes. Each programme of work expands the understanding of the ore from the previous, building more confidence and efficiency when proceeding with the next, ensuring we meet the needs of the client.
Impact
Previous metallurgical testwork had been undertaken by the client but did not meet their grade and recovery targets, particularly the flotation results for the most challenging ore body. SLR was able to confirm the underperforming testwork and from this, develop optimised conditions that achieved targets. This was critical to resolve for the flowsheet development as part of the pre-feasibility study.
The completion of the testwork programmes was done in a timely manner to ensure the client was able to incorporate the results into their pre-feasibility and feasibility studies.