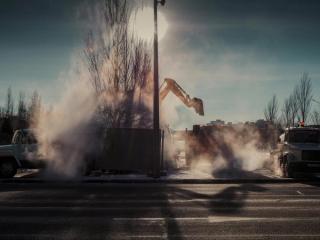
Strengthening supplier engagement: 5 ways companies can facilitate their suppliers’ transition to enhanced ESG performance
- Post Date
- 25 April 2024
- Author
- Chynna Pickens
- Read Time
- 6 minutes
- ESG advisory
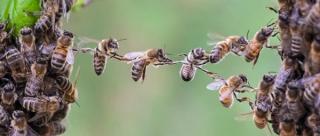
Addressing ESG issues and reducing overall emissions through supply chain efforts is a growing practice across industries. However, to ensure a smooth transition, companies can guide and support suppliers through their transition to cleaner and more ethical business practices.
In 2024, responsible sourcing will continue to grow as formal reporting practices have been implemented in Europe (e.g., CSRD, ESRS, and CSDDD) and ESG ratings bodies in the U.S., such as S&P’s Corporate Sustainability Assessment, are beginning to update their methodology to require a more detailed approach to supply chain management and supplier engagement reporting. Companies will need to be able to assess the environmental and social impact of each of their suppliers down the entire chain. So, the question that companies further along in their ESG journey should consider is:
How can my organization ensure that our suppliers can meet growing ESG expectations?
1. Prioritize and segment your suppliers to determine targets for engagement.
Before beginning engagement with suppliers, it is important to understand your supplier base, particularly which suppliers are more exposed to risk than others and which are more capable of aligning to your organization’s ESG commitments. Prioritizing suppliers in this way will allow for a more targeted and efficient approach during engagement.
For example, if an organization has determined that suppliers in a certain region are not subjected to strict human rights or OHS regulation at the government level, it may be important to prioritize regular auditing or assessment for those suppliers.
2. Develop a supplier code of conduct that is achievable yet actionable.
A supplier code of conduct will allow all suppliers to have a better understanding of expectations specified by your organization. Maintaining a code of conduct will benefit the organization in numerous ways, especially if the organization has suppliers in countries that may not have regulations around environmental or social issues. If the code of conduct is included in contracts signed with the organization, suppliers can also be held accountable if they are not in compliance.
When developing a code of conduct it is important to keep suppliers’ capabilities in mind. By requesting feedback in the form of surveys or interviews, your organization can gather intel on challenges during their transition to more sustainable and ethical practices. This would be an opportunity to learn how to better support suppliers and encourage continued development.
3. Invest in education and training opportunities for suppliers.
Many suppliers, especially those with more complex operations, may have trouble immediately adhering to a supplier code of conduct. By providing opportunities for education and training, suppliers are able to upskill more efficiently. Education and training topics can include, but are not limited to, regulation compliance, reporting requirements, data and documentation gathering, and how to better adhere to the organization’s supplier code of conduct. These trainings can be given in the form of workshops, webinars, and in-person events/conferences. Alongside these opportunities, companies should also consider developing an online platform that suppliers can access at any time with information not only from the company itself, but also other ESG standards and frameworks that support the ESG strategy.
The benefits of educational and training opportunities also include faster response rates when collecting data for ESG reporting, organized and consistent data, and better collaboration between an organization and its suppliers. Increasing engagement and collaboration with suppliers will build trust and better align suppliers with the organization’s ESG strategy.
4. Offer financial incentives and rewards.
When organizations reward their suppliers for their commitment to sustainability, this demonstrates the importance of ESG performance to the organization. Examples of financial rewards include changes in payment terms, access to funding/support, compensation for green products, or payment for performance.
The World Business Council for Sustainable Development found that when providing financial support or incentives to suppliers, organizations can experience improved transparency of the decarbonization efforts, better trust and relationships with suppliers, and a reputational boost when publicizing the efforts of their suppliers [1]. Further engagement can be implemented by surveying suppliers to understand which type of financial incentive would be the most impactful or collect feedback from suppliers after a financial incentive has been distributed to gain insight on how the incentive helped to improve their processes.
It is important to consider how financial incentives are allocated amongst suppliers and to first develop a set of requirements in order to receive an incentive. Some organizations have offered tiered programs, that allow suppliers to monitor whether or not they have met the performance goal to reach the equivalent incentive level. Third-party organizations can also be used here to help companies determine accurate levels of incentives for their suppliers.
5. Continue to implement risk assessments and assess supply chain regularly.
After implementing a supplier code of conduct, investing in supplier education and training, and incentivizing top performance, it is important for companies to also periodically assess supply chain risk. ESG-related risk assessments will use data collection, external audits (typically third-party audits), site assessments and more to determine the risks and opportunities of individual suppliers. This will be an important opportunity for companies to evaluate any suppliers that may be laggards within the supply chain and develop ways to provide support.
Supplier risk assessments can be performed in a variety of ways, however desk assessments such as surveys are typically used. Sometimes organizations develop their own, however many use independent third-party auditing/accrediting bodies such as EcoVadis, ISO Standards, or Higg Facility Environmental Module. Another form of risk assessment also includes on-site assessments by an auditor and can include document reviews, site tours, and interviews with employees or representatives.
Once the organization determines that a company is a laggard, many will develop a corrective action plan, or CAP, which will identify the root cause of the supplier’s risk and provide a strategic plan to mitigate those risks. CAPs can also include on-site collaboration of a designated amount of time that will ensure that suppliers are able to achieve their goals.
Although each of these steps can seem like a sizeable investment for a company, these proactive measures can provide cost savings in the long run, ensure a resilient supply chain, and directly impact communities and the environment local to your suppliers’ operations. Growing regulation will require companies to report on the impacts of their supply chain and progression towards more sustainable and ethical practices. At SLR Consulting, we can provide responsible sourcing services to support you on your journey through supply chain risk identification and management, impact assessments, reporting and more.
-----------------------------------
References
[1] - https://www.wbcsd.org/contentwbc/download/15015/212942/1