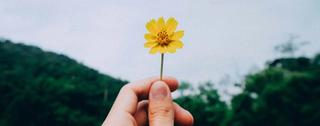
Electrifying mine hauling will boost energy strategy importance
- Post Date
- 12 May 2025
- Read Time
- 13 minutes
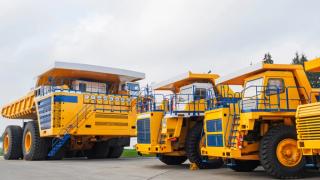
The global mining industry is showing a growing interest in and adopting the use of electric-powered haul trucks, driven by Original Equipment Manufacturers (OEMs), mining companies, and industry alliances. Both underground and open-pit operations are piloting and deploying innovative technologies as part of a new era of cleaner, smarter, and more efficient mine haulage.
When implemented strategically, electrification delivers significant, long-term value:
1. Enhanced productivity through increased speed, continuous mining, and improved acceleration, reducing cycle times.
2. Higher energy efficiency, resulting in lower energy consumption, operating costs, and greenhouse gas emissions.
3. Reduced total cost of ownership (TCO), enabled by lower fuel and maintenance costs and higher fleet availability, utilisation, and productivity.
The path to electrification of mining is complex
Without a deliberate and integrated approach, the transition to fully (or partially) electrify may risk operational continuity through disruptions and financial impacts.
This article explores the strategic and technical considerations for electrifying mine haulage across both open-pit and underground operations, and within brownfield and greenfield environments. The critical importance of a long-term energy infrastructure strategy is highlighted together with a focus on adoption and adaptation principles. As mining operations become increasingly dependent on electric power - both on-site and off-site - companies must align technology choices with energy system development and permitting timelines to secure sustainable, scalable solutions.
Advancements in electrification for open-pit mine hauling
Haulage in large open-pit mines remains dominated by ultra-class trucks, typically with payload capacities between 200 and 370 metric tons, operating continuously in demanding conditions. Depending on OEM, these trucks may have diesel-electric drivetrains, where a diesel engine powers electric traction motors. To transition these systems to full electrification, an alternative power source that delivers continuous high power levels reliably and efficiently is required.
One established technology is the trolley-assist system, first introduced in mining as early as 1967. This system enables trucks to draw power directly from high-voltage overhead lines via a pantograph connection, typically on uphill segments where energy demands are highest. The key benefits of trolley-assisted haulage include:
1. Higher uphill speeds, and productivity, as electric motors aren’t constrained by the diesel engine’s power limits.
2. Lower energy costs, through increased system efficiency and reduced diesel dependency.
Despite its potential, adoption of trolley-assists at scale has been limited due to several key challenges:
1. High capital costs for fixed infrastructure and truck modifications (pantographs and high-voltage electronics).
2. Reduced operational flexibility, as the fixed nature of the infrastructure restricts where trolley segments can be deployed (traditionally only on long-term and/or final pit ramps).
3. Increased operational complexity and safety risks, due to the integration of high-voltage components in active mining zones
4. Other required safety de-risking (BEV specific), due to the potential for arc-flashes, which require engineering and process redesigns, maintenance practices, and facilities
Fuelled by decarbonisation targets and the emergence of battery-electric haul trucks (where trolley systems can play a critical enabling role), new interest from large mining companies including AMSA, Rio Tinto, BHP, Glencore, and Boliden in recent years has reignited development. The emergence of dynamic charging (i.e. batteries recharging whilst trucks are in motion and connected to a pantograph) represents a new innovation in trolley system technology that helps address range and availability limitations of battery trucks as well as enhances utilisation through increased operational continuity (no need to stop for recharging at a station).
To overcome the constraints of traditional overhead trolley systems, companies like Caterpillar and BluVein are pioneering next-generation solutions. These involve a lateral rail system that interfaces with a retractable arm mounted on the truck, providing the following benefits:
• Greater mobility and flexibility within evolving mine plans.
• Improved connection stability, critical for consistent power delivery.
• Higher power throughput, supporting both traction and in-motion battery charging.
These systems are currently in the testing phase and could represent a major step forward in making mine electrification and battery technology viable and economically interesting in open-pit mining.
Advancements in electrification for underground mine hauling
Underground mining operations are uniquely positioned to benefit from haulage electrification both economically and operationally. With ventilation representing a significant cost element in underground mines, reducing the use of diesel-powered equipment directly translates into lower energy consumption, improved air quality, and reduced infrastructure needs.
In recent years, the industry has seen rapid progress in the development and deployment of battery-electric vehicles (BEVs) for underground material movement. Several OEMs have introduced electric trucks and loaders specifically designed for underground conditions, offering competitive performance while eliminating diesel emissions at the source.
Key drivers of underground electrification include:
• Reduced ventilation requirements, as BEVs eliminate diesel exhaust and lower ambient heat generation.
• Potentially lower operational costs, through decreased fuel consumption, maintenance, and ventilation-related energy use.
• Improved working conditions, resulting in a safer, quieter, and healthier environment for workers.
• Regulatory alignment, supporting compliance with increasingly stringent environmental and occupational health standards.
However, successful underground electrification hinges on several key factors:
• Battery strategy: Selecting / developing the right battery to match the operational profile, shift patterns, charging strategy, and safety requirements.
• Charging infrastructure: Designing charging systems - whether fast-charging, battery swapping, or a battery swap dispatch system - that align with shift patterns, production schedules, and mine layout.
• Thermal management and fire safety: Managing heat generation, ventilation, and fire risk in enclosed environments with strict safety regulations.
• Power infrastructure: Ensuring sufficient electrical capacity and redundancy within the underground network, especially as multiple systems compete for power.
Leading mining companies are already implementing pilot projects and full-scale deployments of electric underground fleets. In parallel, partnerships between miners, OEMs, and technology providers are driving innovation across the battery, charging, and power management ecosystems.
Reliable electricity strategy for mining
As mines electrify their hauling systems, driven by emissions abatement, energy increasingly transitions from merely a utility to a core operational dependency and a strategic enabler. To support this transition, mining companies must develop comprehensive, forward-looking energy strategies that consider capacity, reliability, cost optimisation, and sustainability in equal measure.
A well-structured energy infrastructure plan should address four critical dimensions as summarised in the following table.
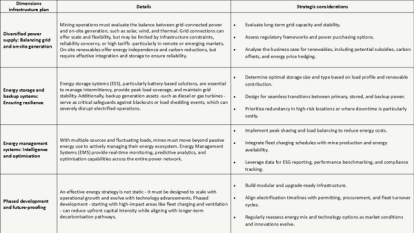
Ultimately, powering an electrified mine is not just a technical challenge but rather a strategic opportunity. The companies that succeed will be those that treat energy not as a constraint, but as a competitive advantage — planning holistically, investing wisely, and building resilient systems that support productivity, sustainability, and long-term value creation.
Brownfield vs Greenfield implementation considerations
Electrification strategies must be tailored to the specific context of each mining operation. A key factor in setting direction is whether the site is a brownfield or greenfield project. Each scenario presents distinct challenges, opportunities, and strategic considerations.
Greenfield: Electrification by design
Greenfield projects offer a unique advantage, representing the opportunity to incorporate and embed electrification from inception. Mine design and planning, infrastructure, fleet selection, power systems, and competencies can be applied holistically based on electrification and scaled accordingly for future development.
Key advantages include:
• Optimised mine planning for electric fleets, including cycle times, haulage distances and routes, dimensioning (size and life cycle), logical charging points, and strategic segments for dynamic charging for open-pit.
• Right-sized energy infrastructure, such as substations, distribution networks, and renewable integration, designed to meet future electric load profiles.
• Cleaner permitting narrative, aligning with ESG goals and investor expectations from day one.
• Integrated systems, allowing automation, digitalisation, and electrification strategies to evolve in parallel.
In many jurisdictions, electrified greenfield operations also benefit from accelerated permitting pathways and stronger public support, particularly when paired with commitments to renewable energy sourcing and emissions reduction.
Brownfield: Strategic retrofit and transition planning
In contrast, brownfield mines must navigate the complexities of operational transformation and transition associated with retrofitting and / or introducing electrification into an active operation. This requires a delicate balance to ensure operational continuity and minimise impacts on productivity and production targets whilst dealing with legacy diesel fleets and established infrastructure at the same time as maintaining an acceptable investment case.
Key considerations for brownfield transitions include:
• Phased fleet replacement, balancing capital constraints and residual asset life with the introduction of electric vehicles.
• Capital considerations, understanding equipment replacement schedules, and depreciation as a function of the investment case and productivity’s full potential (including inherent limitations resulting from levels of mixed electric and diesel fleets where necessary).
• Infrastructure upgrades, such as adding charging stations, strengthening power distribution, and managing peak loads.
• Workforce adaptation, including retraining for electric equipment operation, maintenance, and safety.
• Change management, ensuring cross-functional alignment and minimising operational disruptions during the transition.
While brownfield electrification may require more careful integration, it can still deliver strong returns - especially in mines with extended life-of-mine horizons. Transition plans should be anchored in long-term economic modelling and supported by flexible, modular technologies that can scale over time. An interesting concept is to separate out a new development of the mine and implement it as an electrified greenfield project.
Effectively, greenfield projects allow companies to design for electrification, while brownfield operations demand a strategic, incremental transformation. In both cases, aligning technical planning with financial, environmental, and operational realities is essential to unlocking the full potential of electric mine hauling.
Adoption and adaptation as part of the energy transition
A clear electrification strategy is fundamental to an organisation’s energy transition journey. Whether brownfield or greenfield, electrifying mine sites represents new processes, competencies and skill sets, and equipment / systems / infrastructures. These must be defined, designed, implemented, and operationalised to ensure health and safety together with operational continuity. This presents certain challenges given some of the nascent characteristics associated with new technologies and innovation that are part of electrification in mining. One of these is directly related to the Technology Readiness Levels (TRLs) regarding both who is driving advance (OEMs vs. mining companies) and how to accelerate.
In this context, the electrification strategy needs to consider and balance new technologies with risk tolerance. This means clearly identifying and positioning as innovators, early adopters, the early majority, the late majority, or the laggards.
Whether a pioneer (innovators and early adopters) or fast-follower (early majority onwards), it’s a risk-reward position (i.e. shaping direction and capitalising on early gains, but confronting the typical “chasm” in early adoptions, vs. taking the “wait and see” approach, with less input in the direction). Regardless, achieving energy and emissions excellence as part of the energy transition presents a platform for understanding the incentives behind timely adoption and adaptation to ensure advancement and continued inertia moving forward.
To do this requires bringing together the dimensions of economics, energy, and emissions, and understanding the trade-offs between each. Balancing the tensions with the synergies occurring at the intersections defines the business value, underpinned by how adoption and adaptation form part of the electrification strategy. This can be translated, simplified, and viewed through the lens of de-risking, influencing, and accelerating. These function as key drivers for positioning adoption and adaptation principles as part of the electrification strategy, as defined in the framework below.
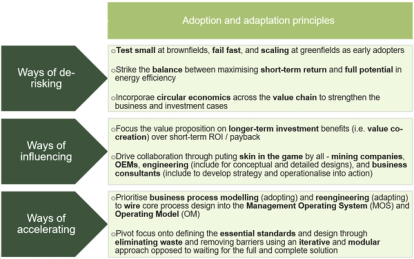
The electrification of mine hauling is no longer a distant aspiration but rather a tangible, accelerating shift reshaping how mining operations are designed, powered, and optimised. From underground to open-pit mines, and across both greenfield and brownfield developments, electrification offers clear, compelling benefits: improved productivity, lower operating costs, enhanced worker safety, and significant emissions reductions.
However, these benefits are not automatic. They require careful planning, cross-functional alignment, and long-term strategic thinking. This is particularly the case when it comes to energy infrastructure. As dependence on electricity increases, so does the importance of a resilient, flexible, and cost-effective power strategy.
Mining companies must take a proactive approach:
• Design electrification into greenfield projects from the start.
• Retrofit brownfield operations through phased, business-aligned transitions.
• Build diversified, future-ready energy systems that integrate renewables, storage, and smart controls.
• Treat energy not simply as an input, but as a lever for performance, competitiveness, and sustainability.
• Understand how adoption and adaptation principles form part of their electrification strategy as drivers for de-risking, influencing, and accelerating the energy transition.
Electrified mine hauling is not just more efficient, but rather it’s smarter, cleaner, and better positioned for the demands of a decarbonised world. Those who lead this transition will define the next era of mining.